Construction and demolition waste currently contributes to at least 40 per cent of Australia’s landfill. With many homes in Australia designed for just a 30-year life span, it’s time to rethink the future of housing if we want to reduce our resources waste and live in homes that last.
Timothy O’Grady and Roberto Minunno from the Curtin University Sustainability Policy (CUSP) institute may just have the answer to Australia’s housing state. Under the supervision of CUSP Director Professor Greg Morrison, the PhD researchers have designed the Legacy Living Laboratory (L3) – a building constructed from sustainable materials that not only looks great, but can be easily ‘packed up and down’ and relocated as required. Forget demountable buildings, enter modular living.
“What we’re trying to do with the living lab is build a circular economy building. Circular economy basically means ‘reduce, reuse, recycle,’” O’Grady explains.
“With urban sprawl, it’s not feasible to keep building standard houses, only for them to be knocked down or renovated decades later. There is no point in creating all that waste.
“But if those buildings could be disassembled and transported instead of demolished, that’s a more viable option.”
Circular economy replaces the traditional model of ‘dig, process, use, chuck’ with one that returns materials back into the system, thus extracting more value while reducing our carbon footprint. O’Grady and Minnuno published a research paper last year detailing how circular economy can be successfully applied to modular buildings, with L3 as the prototype.
Their research is backed by Curtin, LandCorp and Fleetwood, a Perth-based modular construction company, and has sparked the interest of the state’s housing and construction industry. So far, 15 companies have partnered with O’Grady and Minunno to contribute a range of innovative products, materials and technology to construct L3.
By definition, L3 is your typical modular building. Modulars comprise boxes or modules made from steel frames that are built offsite in a factory environment before being trucked to site and connected together to create a finished building. L3 is made up of eight rectangular modules; five fit together to form the ground floor, and three modules fit on top to make the second storey.
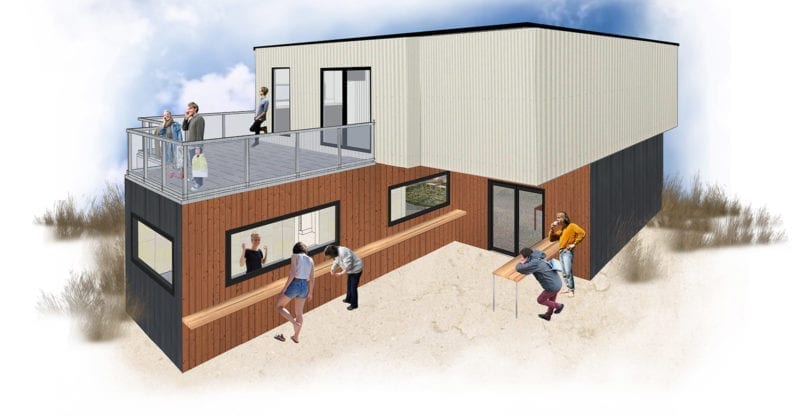
“Modular construction has been shown to have many benefits, such as reduced construction periods resulting in minimal site disruption,” O’Grady says.
“Other benefits include better build quality and reduced waste due to standardised manufacturing techniques.”
What makes L3 different is it’s the first of its kind in Australia to be constructed from salvaged or recycled materials.
For example, its foundation steel frames were rescued from the scrap heap. The ceiling panels are made from recycled plastic bottles, which are also sound absorbent. The carpets were donated from a refurbished building that was newly leased and consequently redecorated. The stairs that connect its two storeys are reclaimed steel from a failed building project, and the stair treads are 100-year-old jarrah sourced from a disused factory in Fremantle.
It may sound like Frankenstein’s creation but the end product is an original, organic structure that boasts form and function.
“While it may not be typically beautiful, you can see the work that has gone into it, you can see it’s been reborn,” O’Grady says.
More importantly, O’Grady and Minunno’s latest research has shown that due to its disassembly and reuse, L3 saves 16 per cent of greenhouse gas emissions compared to the best common practice of recycling building materials.
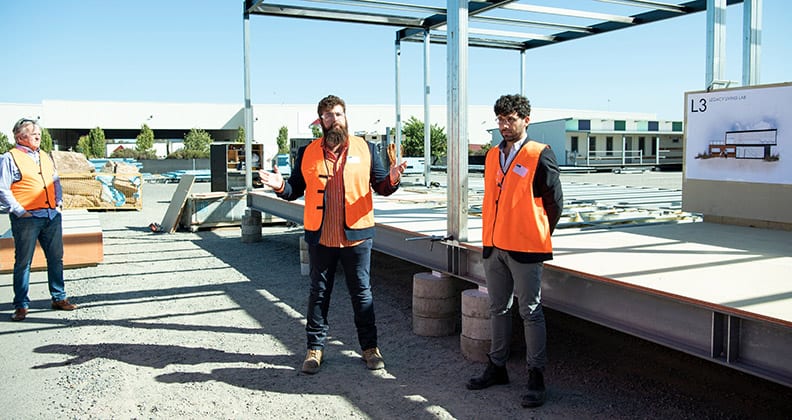
L3 is a step-change for housing construction and sustainability, but despite its evident benefits, O’Grady has faced opposition throughout the design and building process.
“The challenging thing has been trying to get people to do things differently. A lot of the time people say ‘no’ because it’s just not how things have ever been done.
“But I’m not here to replicate what has already been done, I’m here to try and push the boundaries of what we can do.”
Indeed, O’Grady says Australia lags behind many other countries when it comes to modular building, and sustainable modular building in particular. Currently, modular accounts for just six per cent of the nation’s construction market share. But with Australia’s housing affordability crisis, coupled with population increase and dwindling natural resources, there has been a growing interest from government and industry to look at smarter ways to build.
While L3 holds promise, O’Grady explains there is still a way to go to ensure waste materials are readily available.
“With circular economy, you need to close the supply chain. Right now, there is no standardised way of salvaging or sourcing building material waste and supplying it to industry.
“But there is certainly an opportunity there to connect the two sides and put that ‘waste’ back into the economy.”
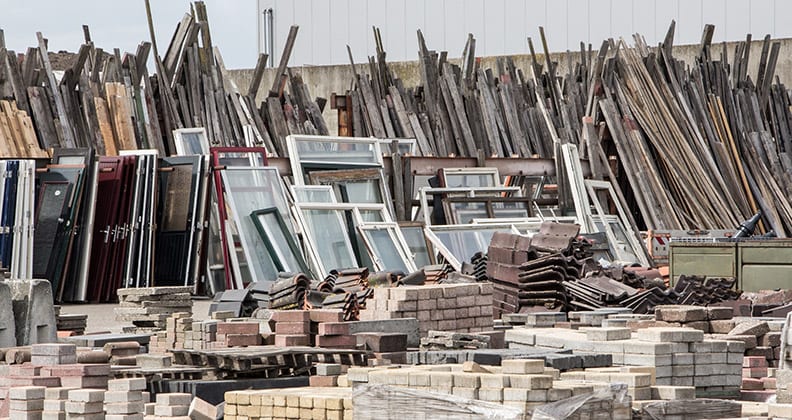
L3 is set to test just how economical ‘rubbish’ can be when it’s transported to a LandCorp-donated site at the East Village in Fremantle in August. For the next two years, it will be tested, assessed and modified by industry, making it a living experiment in sustainable construction and design.
The lab will also feature an iHUB facility, connecting Curtin with four other Australian universities – the University of Queensland, UNSW Sydney, Swinburne and Monash – enabling test data to be instantly collated and shared.
For O’Grady, a crucial aspect is that L3 will be open to the public during its testing phase, ensuring people can learn about circular economy and experience first-hand the future possibilities of modular living.
“A lot of people don’t actually know that there are others ways to build, as it’s never been presented as an option,” he says.
“This will be a way to demonstrate that you can build differently.”
O’Grady and Minunno’s PhD is funded by the ARC Centre for Advanced Manufacturing of Prefabricated Housing (CAMP.H). O’Grady is also partnered with Quantify Technology as part of a state government PhD Fellowship program that aims to reduce energy consumption by advancing smart home technologies.
Learn more about the Legacy Living Laboratory.