Curtin-developed laser scanning technology is helping mining companies around the globe save energy, reduce downtime, improve safety and maximise the life of valuable equipment.
In mineral processing, raw ore is generally crushed into progressively smaller pieces using a rock crusher, and then ground into a powder in a grinding mill before further processing. Both grinding mills and crushers use internal replaceable liners to protect the outer shell from abrasion damage. As these wear over time they need to be regularly replaced.
Since mills and crushers operate 24/7, replacing a worn liner requires significant shutdown time. Replace them too early and the costs increase. Replace them too late, and grinding performance and energy efficiency deteriorates, while you run the risk of catastrophic failure.
The traditional approach to monitoring is for a person to climb inside a shutdown mill and physically measure the thickness of the liner at several points; these measurements are assumed to be representative of the condition of the liner as a whole. Stopping a mill periodically to visually inspect the internal liner is difficult, expensive, inherently dangerous, and inaccurate. So in some cases no monitoring is performed at all.
Because the consequences of a catastrophic failure are so high, conventional shutdown and reline schedules are generally extremely conservative, leading to inefficient use of liners and lower levels of equipment availability.
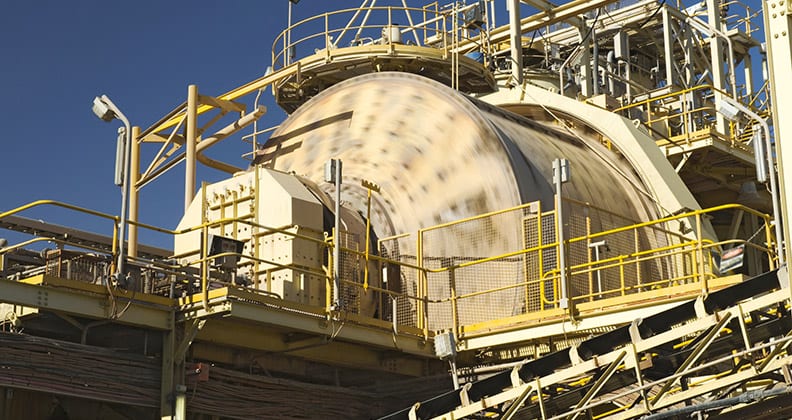
From 2001 Dr Derek Lichti, Dr Mike Stewart and Dr Jochen Franke began investigating the use of terrestrial laser scanners to map surfaces and detect surface deformation. By scanning a laser beam across an object and recording the reflected signal from a ‘cloud’ of points, they could build up a 3D picture of the surface with a precision of ± 0.5 mm.
This research led to unique technology for 3D spatial data collection of the entire environment surrounding a laser scanner inserted into a grinding mill or crusher. Ten million spatial data points covering an entire liner surface can now be collected in less than five minutes, without requiring a person to physically enter the mill.
Smart algorithms extract useful information from the dataset, such as the thickness, weight and condition of the entire liner surface, along with high wear zones and critical wearing areas. This data is then used to make intelligent reline forecasts.
Based on this research, Scanalyse was established in 2005. The first mature product, MillMapper, was released in 2007, encompassing data collection, development of a 3D model of the mill interior, a time-series analysis database and expert commentary highlighting and interpreting the critical information identified for mill operators.
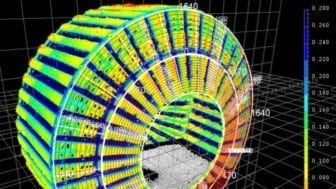
In 2009 Scanalyse applied the same approach to the measurement and monitoring of crusher liners, although product development was complicated by the need to collect and combine multiple datasets from different locations to give a complete model. The two separate wearing surfaces in a crusher also need to be positioned in real space and analysed to give a complete picture of the crusher interior.
MillMapper and CrusherMapper were world firsts for in situ measurement, modelling and management of grinding mills and crushers. These wear and performance management tools allow rapid and precise condition monitoring, and forecasting of the maintenance procedures necessary to ensure optimum performance and usage. Their use also enables the design of more efficient liners that better withstand wear throughout their lifecycle.
Impacts include:
- reduced energy use (roughly 60 per cent of a minesite’s energy consumption is used in crushing and grinding ores)
- reduced downtime (in an industry where downtime on a mine can cost $100,000 an hour)
- dramatically reduced risk and potential loss due to catastrophic failure
- increased useable lifetime of mill liners and maximised financial efficiency of replacing liners
- increased safety, by removing the need for personnel to enter mills and crushers to carry out manual inspections.
More accurate forecasting of relines is allowing companies to incur less maintenance downtime, increase equipment availability, achieve significant extra throughput (and revenue) and more efficiently use resources. Some minesites have been able to double the life of their crusher liners, resulting in up to 2.5 days of extra production per annum as a result of less downtime. The increase in production is valued in the millions of dollars per annum per site. Other minesites have narrowly avoided catastrophic mill failures as a result of timely analysis and warnings given by Scanalyse; a catastrophic failure of a SAG mill can cost between $50,000 and $100,000 per hour in lost production, and can take days or weeks to rectify.
MillMapper and CrusherMapper have significantly improved operational best practice in crushing and grinding circuits with respect to safety. Laser scanning now completely eliminates the inherent risk to personnel by removing the need for confined space entry to manually inspect mill and crusher interiors.
By 2013, Scanalyse had conducted over 1,000 mill or crusher scans for 57 clients, and grown to service approximately 25 per cent of the Australian mill and gyratory crusher condition monitoring market. It employed 39 people in offices in Perth, Australia; Santiago and Antofagasta, Chile; Salt Lake City, USA and Toronto, Canada. Collectively these offices served mineral processing operations of some of the world’s leading mining companies throughout Australia, Asia, Europe, North and South America and Africa.
Clients in Australia have included BHP Billiton, Rio Tinto, Xstrata, Newcrest, Newmont, Barrack and Minmetals, while overseas clients have included Kinross, Teck Resources, Antofagasta Minerals, Anglo American and Cliff Resources.
In 2013, Finnish minerals and metals processing technology and services supplier, Outotec, acquired Scanalyse in recognition of the technology’s immense potential in the global market. Outotec was seen as an ideal vehicle for the technology to achieve further market penetration, following its rapid acceptance by the minerals industry. At the time of ownership transfer, Scanalyse’s revenue had grown to nearly $10 million in 2012/2013.
In the first 12 months after acquisition (to mid 2014), Scanalyse technology was rolled out across Outotec’s distribution channels worldwide.
Scanalyse’s successful path from research to implementation and impact has been recognised through a number of awards from 2007, culminating in a 2013 Australian Museum Eureka Prize, the Rio Tinto Eureka Prize for Commercialisation of Innovation.